Founded in 1970 Esquire Glass has become one of the UK’s leading independent glass processors.
Their core business is in the production of processed glass panels for the kitchen, bedroom and bathroom industry. However, since 2002 substantial investment in a second factory and ‘state of the art’ glass processing plant has led to the company’s accelerated growth into new markets.
Their newest investment has been on a cutting edge finishing system from Giardina Group and their UK partners, Schuberts.
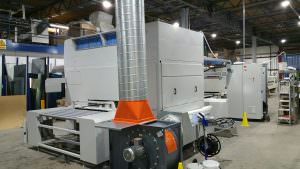
Running with waterbased coatings, the new Giardina system is capable of using both solid and far more difficult metallic colours. Fitted with 2 independent spray circuits, the switch between colours and coatings is very quick, meaning the customer can do both long and short runs of glass. All of the Wagner guns have the ability to run different tips and pressures, making the coating control very accurate.
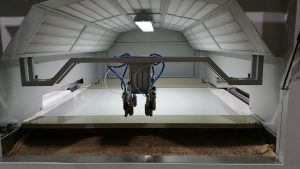
The Dualtech 416 machine has full belt overspray recovery system, meaning wasted coating can be safely removed from the main belt, filtered and re-introduced into virgin mixes. The recovery system, unlike other systems relies on a series of rubber squeegees that gently, but effectively removes paint, rather than harsh metal blades that scrape and damage the belt over time. This guarantees the longevity of the Giardina belt.

The machine also boasts double filtration for the air input system, making the spray zone a clean zone, meaning reworks are a thing of the past.
On the extraction side, there are triple levels of filtration, ensuring incredibly low particulate emissions to atmosphere.
The touchscreen control panel gives the operators fine control over line speed, spray guns, circuits, pressures, gun heights and many other key parameters used for coating – all at the touch of a finger!
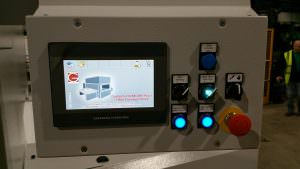
Once sprayed, the glass goes through a flash-off section and then on to a combination drying oven. The glass comes off the end of the line perfectly coated, dry and ready to handle and with a footprint of just 14m from end to end, it really is a compact, high production finishing system.
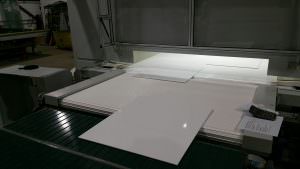
Paul Lockett, MD at Esquire says:-
“ Realising we (Esquire Glass) needed to be more flexible in the painting of our glass products, we spent last summer conducting due diligence on various systems. We found the Giardina system in collaboration with Schuberts UK to be the most effective for our needs. It was installed at the end of Jan ’18 and has already shown huge benefit by taking our production from 400 to 1600 pieces per shift. So far, we are very happy with the machine and are looking forward to developing it’s use over the coming year”
For more information on high quality glass processing and painting, email Esquire Glass sales@esquire-glass.co.uk
For more information on Giardina range of finishing equipment email sales@schuberts.co.uk